Custom Injection Molding Features
High Efficiency
|
High Quality
|
Enhanced Design Flexibility
|
Injection Moulding reduces the amount of time that it takes to make the parts. not only increase productivity also keep costs low.
|
Uniform thickness are no structural deficiencies that could cause problems down the line. the tight tolerances of molds make sure that parts meet industry standards.
|
Allows for greater design freedom than traditional manufacturing methods, making formerly impossible designs a reality.
|
Our Injection Molding Processes

|

|

|
1. Product Design help to develop and evaluate your new products quickly,economically and with less risk.
|
2. DFM Analysis Comprehensive analysis product manufacturability and optimization recommendations for your design.
|
3. Mold Flow Analysis Use CAE technology to simulate the real Injection molding process before Injection mold making
|

|

|

|
4. Mold Design Our molds last 50% Longer than other Molds, they can run up to 15-20 years in most cases.
|
5. Injection Mold Making We have our own mold making factory,This will ensure the mold quality of all manufacturing processes.
|
6. Molding Sample Few or A dozen samples should be produced for assembly/functional testing before mass production.
|

|

|

|
7. Prototype Molding Save development cost, Validate/testing your product/ design functional implementability
|
8. on-demand Molding Machines ranging from 30-1300 tons, 24/7/365 operatons, There are hundreds of material options available.
|
9. Delivery We cooperate with logistics companies to deliver goods to your destination quickly and safely.
|
Materials Used For Plastic Injection Molding
If you’re not sure what material to choose for your design, our engineers with decades years of plastic injection molding service experience will guide you to the right position.
>Acrylonitrile butadiene styrene (ABS) |
>Polypropylene (PP) |
>Thermoplastic elastomer (TPE) |
>Polycarbonate (PC) |
>Polyethyelene (PE) |
>Thermoplastic polyurethane (TPU) |
>Polystyrene (PS) |
>Polyoxymethylene (POM) |
>Polyurethane (PU) |
>Nylon polyamide (PA6, PA66, PA12) |
>Polyphenylene oxide (PPO) |
>Polybutylene terephthalate (PBT) |
>PC/ABS |
>Low Density Polyethylene (LDPE) |
>Polyvinyl chloride(PVC) |
>PA+30GF/50GF |
>High Density Polyethylene (HDPE) |
>Polyethylene Terephthalate (PET) |
>Acrylic (PMMA) |
>Polyether ether ketone(PEEK) |
>PBT Glass-Filled |
>Polyphenylenesulfide (PPS) |
>UHMW |
>Polyphthalamide (PPA) |
Surface Finishes of Injection Molding
The process includes various steps, from injection mold tooling to entire plastic injection molding. Surface finishes of molds are processes typically carried out during production. At our company, we perform the specific surface treatment after the injection molding process according to customer requirements
Reference plate
|
Types of Finishes
|
SPI
|
Description
|
Applications
|
Surface roughness
(Ra µm)
|
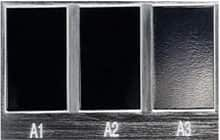 |
Diamond |
SPI-A1 |
#3, 6000 Grit Diamond Buff |
High polish |
0.012- 0.025 |
SPI-A2 |
#6, 3000 Grit Diamond Buff |
High polish |
0.025-0.05 |
SPI-A3 |
#15, 1200 Grit Diamond Buff |
High low polish |
0.05-0.10 |
|
|
|
|
|
|
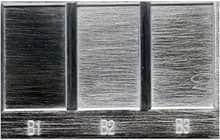 |
Paper |
SPI-B1 |
600 Grit Paper |
Semi-Glossy |
0.05-0.1 |
SPI-B2 |
400 Grit Paper |
Semi-Glossy |
0.1-0.15 |
SPI-B3 |
320 Grit Paper |
Medium low polish |
0.28-0.32 |
|
|
|
|
|
|
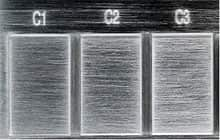 |
Stone |
SPI-C1 |
600 Stone |
Matte parts/Low polish |
0.35-0.4 |
SPI-C2 |
400 Stone |
0.45-0.55 |
SPI-C3 |
320 Stone |
0.63-0.7 |
|
|
|
|
|
|
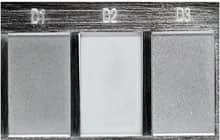 |
Dry Blasted |
SPI-D1 |
Dry Blast Glass Bead |
Sandblasting |
0.8-1 |
SPI-D2 |
Dry Blast #240 Oxide |
1-2.8 |
SPI-D3 |
Dry Blast #24 Oxide |
3.2-18 |